Spécialisé dans la fabrication d’électrolyseurs haute température pour la production d’hydrogène décarboné dans l’industrie, Genvia va tester un démonstrateur sur le site lozérien d’ArcelorMittal. L’objectif est de réutiliser la chaleur de l’usine pour abaisser le coût de la molécule d’hydrogène. Un pas important en vue de la commercialisation de la technologie de Genvia, toujours en développement.
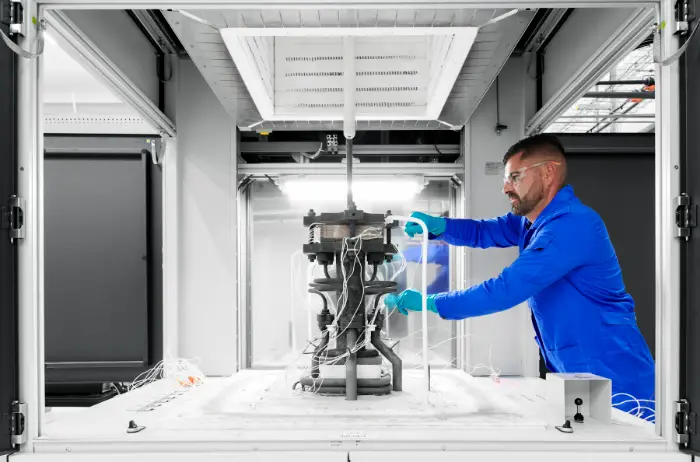
Alliance industrielle entre deux sites historiques de Béziers et Saint-Chély-d’Apcher. Récupérer la chaleur d’une aciérie, pour la transformer en hydrogène décarboné. C’est l’objet du partenariat, signé ce 4 novembre à Béziers entre Genvia, startup industrielle spécialisée dans la fabrication d’électrolyseurs haute température, et ArcelorMittal. Un démonstrateur de Genvia, baptisé SOEL200, incluant des unités de récupération de chaleur et de purification et compression d’hydrogène, va être testé à partir de fin 2025 dans l’usine de l’aciériste à Saint-Chély-d’Apcher (Lozère), produisant des aciers électriques. Il produira de l’hydrogène par électrolyse de vapeur d’eau, en exploitant la chaleur résiduelle de l’usine. Ce sera l’un des premiers démonstrateurs installés sur site, pour un test en situation réelle. Sur un marché international bagarré, marqué notamment par la concurrence de Sunfire, Florence Lambert, PDG de Genvia, place sa technologie « sur le podium mondial. Nous visons le marché de la décarbonation de l’industrie. Transformer la chaleur industrielle permet de faire tomber le coût de la molécule d’hydrogène, car nous utilisons moins d’électricité », explique-t-elle aux Echos.
Cet équipement, assemblé à Béziers, sera composé de plusieurs modules de taille imposante (15 mètres sur 20 mètres), pesant plusieurs tonnes et comprenant des éléments (stacks) en céramique et métal.
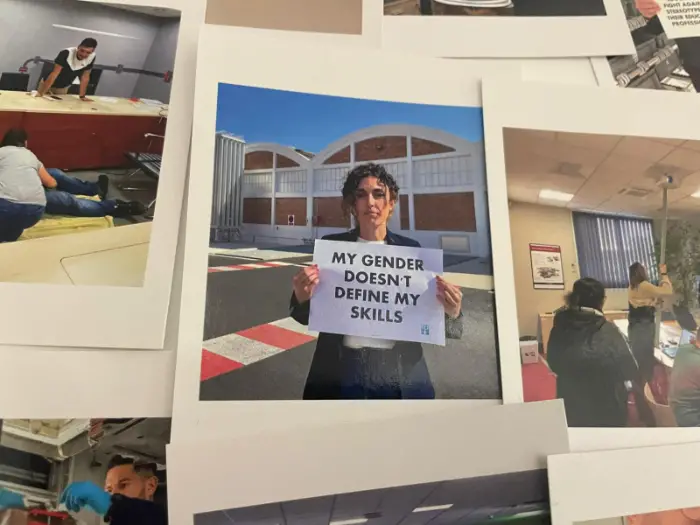
Premiers pas vers une activité industrielle. Les travaux de génie civil se dérouleront l’an prochain dans l’usine d’ArcelorMittal. Avec une capacité de production de 300 kW, soit 200 kilos d’hydrogène par jour, le démonstrateur « pourra couvrir la quasi-totalité des besoins énergétiques de l’usine », souligne l’ingénieure. Pendant la durée de l’essai, l’hydrogène traditionnel, produit par reformatage de gaz naturel, sera remplacé par de l’hydrogène bas carbone, via électrolyse. Les deux pourront aussi être couplés à la demande. « C’est une opportunité pour l’utilisation à grande échelle de l’hydrogène dans la sidérurgie », déclare Bruno Ribo, directeur technique d’ArcelorMittal en Europe.
Vers une plus grande puissance. Ce prototype ne correspond pas au produit final ciblé par Genvia. La R&D travaille à la conception d’équipements de plus grande puissance, à même de produire 1 MW, soit 600 kilos d’hydrogène par jour, toujours pour des acteurs de l’industrie. Genvia entend intégrer sa technologie dans les process industriels et les circuits de chaleur de ses clients. C’est le cas avec Airbus, dans le cadre des procédés de fabrication des carburants du futur. La technologie de Genvia est, selon Florence Lambert, « éprouvée, après plus de 10.000 heures cumulées. Il n’y a plus de verrou. Nous en sommes au stade des tests opérationnels et de recherche de la performance maximale dans le mode de fonctionnement ».
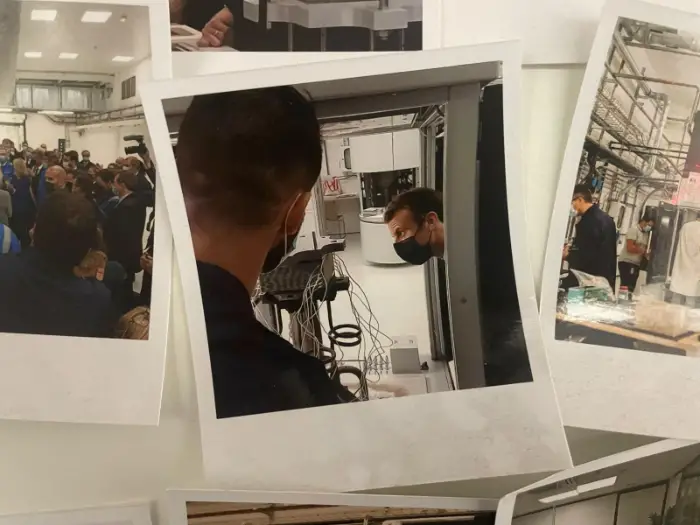
À Grenoble se trouvent les services R&D et V&V (Validation&Verification). Les stacks assemblés à Béziers sont ensuite « maltraités, triturés. Les équipes de Grenoble leur font passer des heures dans des fours, pour éprouver leur robustesse. Et elles les renvoient à Béziers avec des préconisations d’améliorations ». Le site de Clamart est, lui, dédié à l’ingénierie, (partie aval de la production, plus proche du marché).
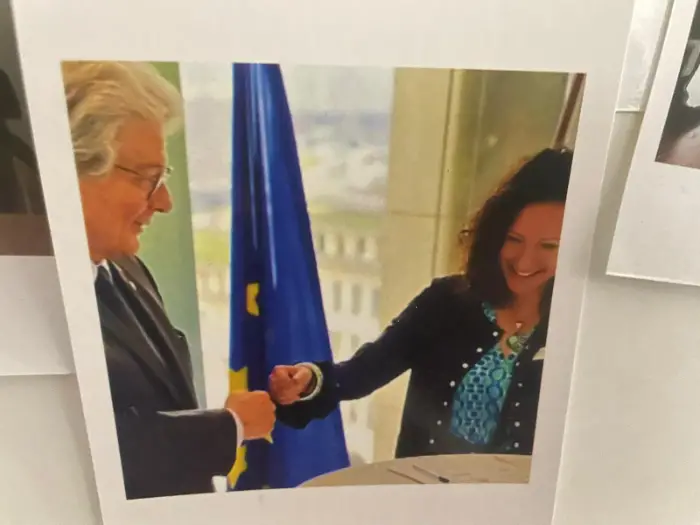
Dérisquer la technologie. « On est au même niveau d’avancement que SunFire. Aucun de nous deux n’est déployé chez un client. ArcelorMittal est un partenariat de test. Ce que l’on cherche, c’est de dérisquer la technologie sur un site industriel, la tester pendant des milliers d’heures, tester et évaluer son rendement, avant de pouvoir le vendre », explique Florence Lambert.
90 salariés à Béziers. Détenue par le CEA, SLB, Crédit Agricole du Languedoc, Vicat, VINCI Construction et l’ARIS (Région Occitanie), Genvia emploie 170 salariés, dont 90 sur son siège de Béziers. Les effectifs restants sont basés à Grenoble et Clamart. À Béziers, la construction d’une gigafactory est prévue à partir de 2027, en vue d’un passage à une ère commerciale. Le projet est soutenu par l’État dans le cadre de France 2030. L’activité de Genvia est actuellement hébergée au sein du centre technologique de SLB, qui fabrique des équipements pour le secteur de l’énergie.
En savoir plus dans l’article « Hydrogène décarboné : Genvia va tester ses électrolyseurs dans une usine d’ArcelorMittal », paru dans Les Echos le 22 novembre.